UTP Produces Face Shields Using 3D Printing and Laser Cut for COVID-19 Frontliners
With the rising numbers of COVID-19 cases in Malaysia, there is a critical demand of face shields for frontliners at hospitals and clinics.
To help meet the demand, Universiti Teknologi PETRONAS (UTP) through its Engineering, Prototyping & Innovation Centre (EPIC), Centre for Automotive Research & Electric Mobility (CAREM) and Technopreneurship Office members have joined forces to produce face shields using 3D printing and laser cut for Perak.
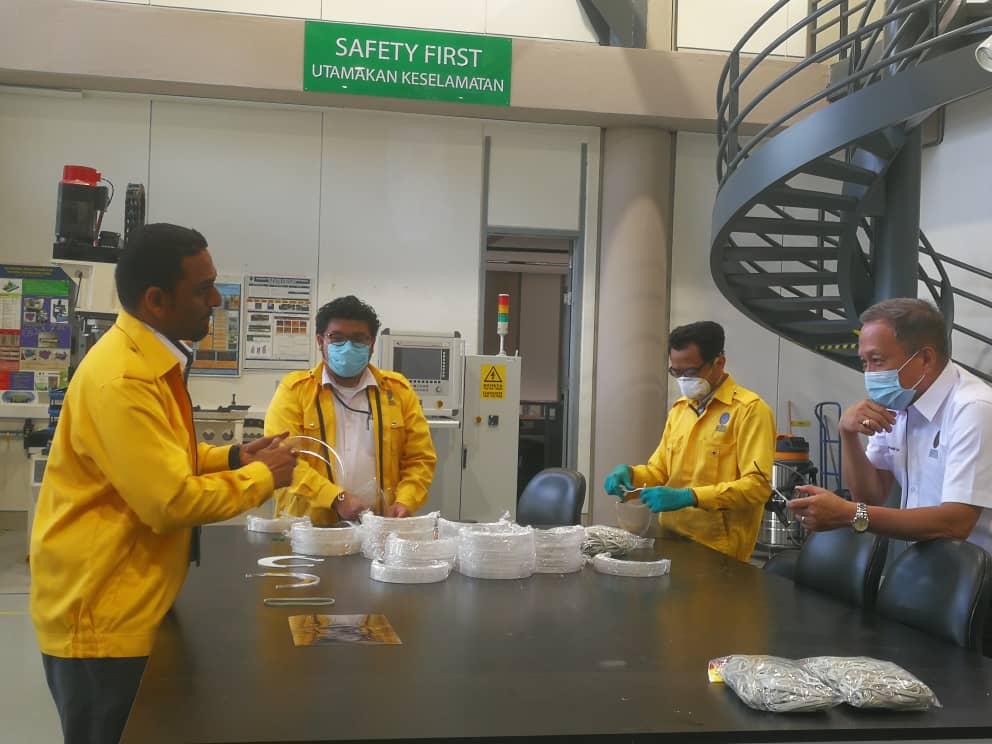
UTP Deputy Vice Chancellor Research and Innovation Professor Ir Dr M Shahir Liew said the university is continuously working closely with the government by contributing products and services developed through research and innovation.
“In this regard, we are responding to the nation's call for help in the fight against COVID-19 by producing face shields for the frontliners as we have the capability, expertise, manpower and facilities. We take the initiative to improve the design of the face shields based on practicality, strength and standard as set by Perak State Health Department (JKN).
“We produce 120 pieces of face shields daily and have, so far, delivered 1100 of them to JKN. JKN will then distribute the face shields to hospitals and clinics in Perak. Our target is to produce 10,800 within 3 months.
“This contribution is part of our university social responsibility's effort to give back to the community. It is also our gesture of gratitude to the frontliners who have been working diligently in battling COVID-19 pandemic," he said.
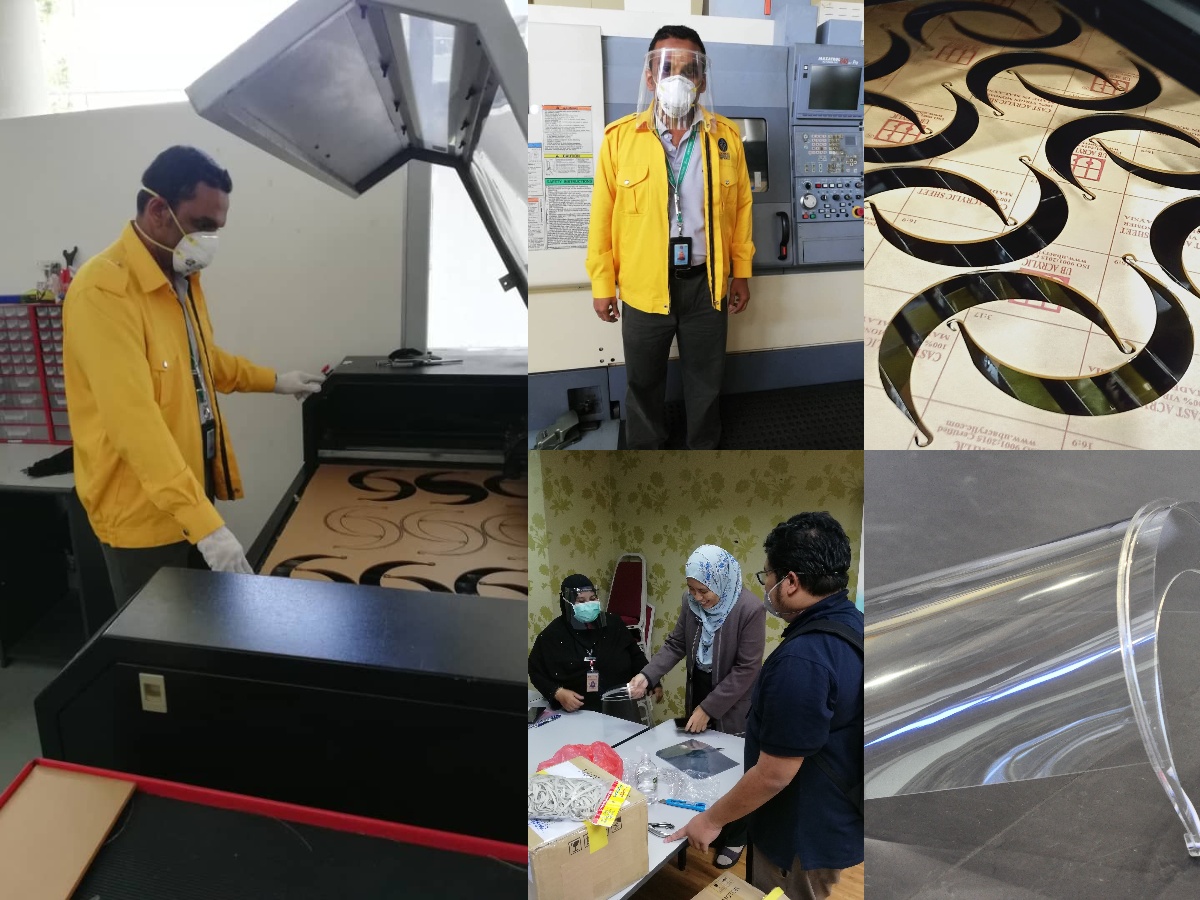
The face shield consists of three components namely a head frame to secure the face shields on one's head, a rubber band to grip the frame around the head and a transparent shield face to protect one's face. The rubber band and transparent shield are common items hence they can be replaced by hospitals and clinics according to their standard operating procedures while the head frame can be re-used after proper standard disinfection method.
“The face shield's frames are fabricated through two methods, laser cut and 3D printing technologies. The former cuts the design on acrylic sheets and can produce more face shields in one run, while the latter produces face shields through additive manufacturing technique using polymer filament and has lower production rate but with less material waste. The production work is carried out daily by eight staff from CAREM and EPIC, on rotation basis, while the design is done from home," said UTP EPIC Head, Nor Shahrul Abu Bakar.